[059] Input Impedance Measurements and Loop Gains
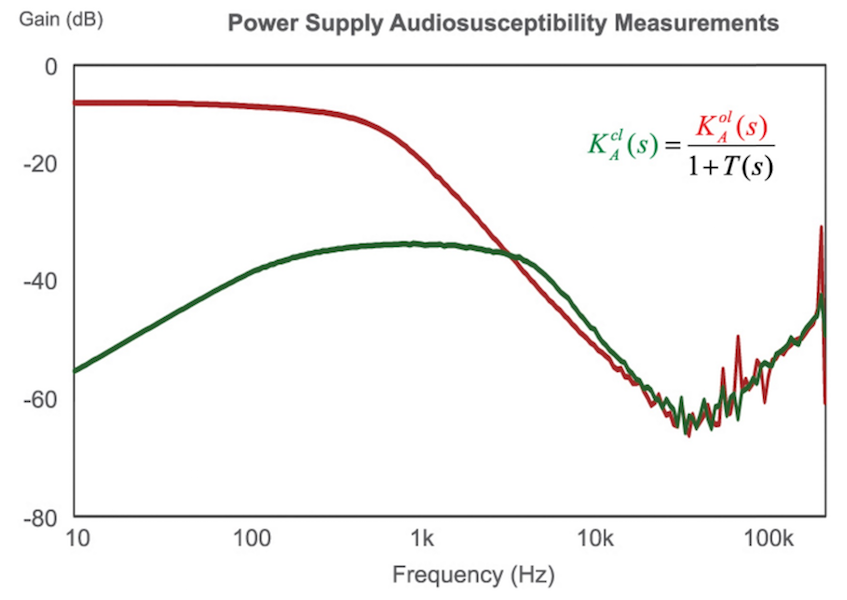
The relationship between loop gain and input impedance
Introduction
In this third part of this series of articles, Dr. Ridley discusses the fourth important frequency-response measurement made during full characterization of a switching power supply. The closed-loop input impedance is measured to be a negative resistance at low frequencies. The input impedance of a power supply is also complicated by the inclusion of input filter parameters in most practical measurements that are made.
Power Supply Transfer Function Measurements
There are four fundamental transfer functions that characterize the small-signal performance of a switching power supply. They are as follows:
- Loop gain and phase – determines the stability of your design, and available margin to accommodate variations in components.
- Output impedance – determines the output regulation, dynamic load response, and susceptibility to complex loading.
- Audiosusceptibility – determines the transmission of noise from input to output.
- Input impedance – determines the sensitivity of the power system to input filter or input power system components.
The first three parameters, loop gain, output impedance, and audiosusceptibility were discussed in the first two articles of this series. It is highly recommended that all three of these measurements are made on every switching power supply that you design and build. The loop measurement is essential to guarantee stability over the lifetime of the power supply, and the output impedance gives comprehensive information about the performance in the presence of load variations. The audiosusceptibility is measured is very useful for showing the rejection of noise from input source to output.
An input impedance measurement gives information about the characteristics of the power supply input terminals. It is usually a requirement of the documentation package in the aerospace industry. As with the audiosusceptibility measurement, a signal must be injected on top of the high-power input rail. Once you have set up your test equipment to do audiosusceptibility measurements, input impedance measurements are straightforward to do.
Input Impedance Measurements
The input impedance measurement can predict how well the power supply will integrate into a system. If the input impedance is too low, it can load down the source and provide adverse system interactions. In order to measure input impedance, a voltage source must be injected in series with the input of the power supply as shown in Figure 1.
Fig. 1: Input impedance is measured by adding a voltage signal at the input terminals of a power supply and measuring input voltage and input current perturbations.
Figure 2 shows how this is implemented practically using a frequency response analyzer and a few discrete devices. The output of the analyzer is connected to wide-bandwidth isolator which is then AC coupled to a FET hooked up as a voltage follower. The size and rating of the FET may vary according to the power level and voltage level of the converter that is being driven. This injection technique is much simpler and more cost effective than inserting a high-power amplifier in series with the input source, and will allow sufficient signal to be injected for most applications.
The only difference between this setup and the setup for audiosusceptibility is that the signals sent to the analyzer are different. For input impedance measurements, Channel B of the analyzer measures the input voltage perturbation, and Channel A measures the input current perturbation. The current is measured with some kind of transducer – either a small sense resistor, current transformer, or active probe.